the hidden cost for US packaging firms
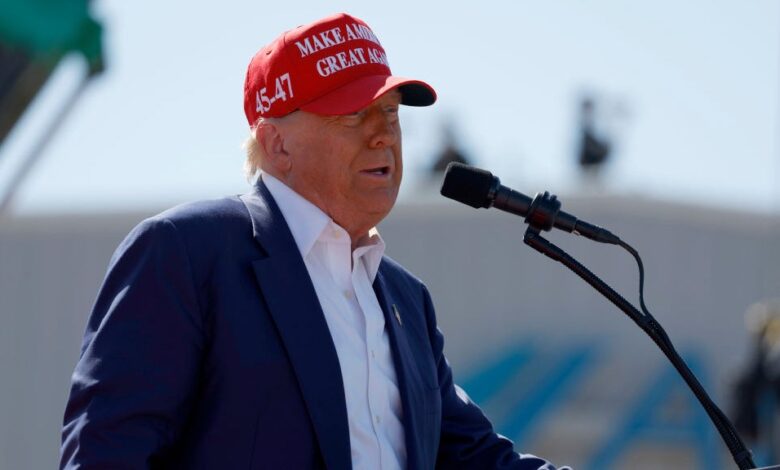
With Donald Trump now in his second term as President of the United States, the impact of his trade policies on the country’s economy continues to be felt, particularly within industries like packaging.
During the US-China trade war of 2018-2019, much of the focus was on disputes over steel, automobiles, and agriculture. However, the consequences for the packaging sector were equally significant, albeit less publicized. Trump’s tariffs reshaped cost structures, supply chains, and long-term strategies for many US packaging firms, creating ongoing challenges that still shape their operations today.
The packaging industry is heavily reliant on raw materials such as aluminium, steel, paperboard, and plastics. When the Trump administration imposed tariffs on aluminium and steel imports in 2018, the costs for these essential components soared. Packaging giants like Ball Corporation and Crown Holdings faced significant burdens as the prices of materials like aluminium for beverage cans and steel for containers increased.
While some companies passed these cost increases onto consumers, others struggled to offset them due to the competitive nature of the packaging market. Smaller firms, in particular, faced difficulties as they lacked the negotiating power to adjust prices or find cheaper alternatives.
Plastic packaging companies, while not directly impacted by steel and aluminium tariffs, felt indirect effects due to retaliatory tariffs on US products disrupting the petrochemical sector and leading to rising resin costs. This added further pressure on an already cost-sensitive industry.
The trade uncertainty introduced by the Trump administration disrupted global supply chains, forcing packaging manufacturers to find alternative suppliers and adjust their sourcing strategies. Companies that historically relied on Chinese imports for machinery or components found themselves at a crossroads, as escalating tariffs raised the cost of essential items and disrupted procurement routes.
With the reduction in global demand for US agricultural exports due to retaliatory tariffs, packaging solutions tied to export markets faced challenges. Many firms had to rethink their investment plans, putting long-term capital projects on hold and incurring expenses to requalify suppliers or diversify sourcing strategies.
Despite the initial justifications for tariffs to encourage domestic production and create jobs, the packaging industry saw limited benefits. The US production capacity for materials like aluminium and steel was insufficient to meet demand, leading to continued reliance on imports at higher prices. The revitalization of the US machinery and equipment manufacturing sector also fell short, with many firms depending on countries like Germany and Italy for specialized machinery.
As we enter April 2025, the legacy of Trump’s trade policies still affects the US packaging industry. Companies have adapted by diversifying supply chains and focusing on automation to offset higher costs. However, many continue to face consolidation or shrinking margins as they contend with the lasting impact of tariffs and trade uncertainty.
The key lesson from this period is the importance of flexibility. Companies that pivoted quickly, diversified sourcing strategies, and adjusted pricing models have weathered the storm better than those slow to adapt. Looking ahead, the packaging industry remains vulnerable to shifts in trade policy and global economics, emphasizing the need for supply chain resilience, strategic sourcing, and technological investment.
Under Trump’s second term, the long-term effects of his trade policies on the packaging industry serve as a cautionary tale. While the immediate impacts of tariffs may have faded, the broader lessons about strategic foresight and adaptability remain as relevant as ever. The packaging industry must remain agile to navigate the uncertain terrain of future trade policies and global economic shifts.